Drones may not replace the honeybee, but dont bet on a future of agriculture that doesnt increasingly depend on their capacity to reinvent 21st century farming.
No ‘game of drones:' The serious future of unmanned aerial vehicles in agriculture
Nefa Berberovic | Richard van Hooijdonk
In field in Prosser, Washington, an eleven-foot unmanned helicopter hovers low above the cherry trees, moving slowly as the downwash from its spinning rotor shakes rainwater from the trees. It’s a test by Washington State University’s Lav Khot, an assistant professor of biological systems engineering at WSU’s Center for Precision and Automated Agricultural Systems (CPAAS).
As any cherry farmer knows, as they reach their ideal ripeness, the sweet fruit’s skin becomes fragile. At that point, rain is a disaster. As the ripe, red, delicate cherries soak up the excess moisture, they swell and split, ruining the harvest.
No cherry farmer hasn’t had his sleep troubled by the sound of coming thunder.
But that’s a nightmare from which drones are waking farmers. Dr. Khot wants to see the rapid adoption of drones replace expensive, dangerous, manned helicopter missions. His goal is to prove that Yamaha’s RMAX can deliver the same results at a fraction of the cost and no risk to human life. And Dr. Khot is just one of the many researchers exploring the future of drones.
As anyone interested in modern agriculture knows, drones are here to stay. These lightweight, agile, inexpensive work-horses quickly moved from combat to farm, a real life example of beating swords into ploughshares. The very qualities that made drones ideal for battlefield reconnaissance make them ideal platforms for other sensors and cameras, too, and it’s now commonplace to see farmers fielding sophisticated drone tech to increase yields and lower costs.
Flying sensors
Indeed, the most familiar use of drones in agriculture takes advantage of their speed and carrying capacity. Fitted with sensitive cameras and sensors, drones can capture crop data in real-time, telling farmers about problems before they become insoluble crises.
For instance, innovations such as Sentera’s Quad Sensor offer farmers a picture of their crops far better than any human eye by using Normalised Difference Vegetation Index (NDVI) and Normalised Difference Red Edge (NDRE) technology. NDVI works because the chlorophyll in plants’ leaves absorbs only the wavelengths of sunlight necessary for photosynthesis, reflecting the remainder like living, green mirrors. NDVI uses infrared cameras to see this reflected light, and the more reflected in the infrared spectrum, the healthier the vegetation below. NDRE is merely a formula for measuring the ratio of reflected and absorbed light, a shorthand metric that tells farmers about crop health by comparing the two numbers.
Together, they can tell a farmer what he needs to know while there’s still time to take action. You can think of these together as an early warning system for crop failure.
As Salman Siddiqui explained to The Guardian, “Using near-infrared, you can identify stress in a plant 10 days before it becomes visible to the eye [...] When a plant goes into stress, it’s either due to a water or fertiliser shortage, or because it’s being attacked by a pest. Photosynthetic activity decreases and that affects the chlorophyll. That’s what the near-infrared sensor can detect, but our human eye can’t see it until it’s more advanced.” Dr. Siddiqui is the head of the International Water Management Institute (IWMI), and though his primary concern is water use, he knows that pests are plague for farmers. “If a crop is being attacked by insects, the whole area can be affected, not just one farmer. With UAVs, if you can figure this out before it spreads, you can save the whole area.”
It’s easy to understand, then, why farmers were quick to embrace drones as agricultural reconnaissance platforms. With these eyes in the sky, they can now know if their crops are happy, see where problems are developing, and take preemptive action.
Exciting as this is, however, it’s only the beginning.
Automation: a farmer’s best friend
Most agricultural drones need a licensed pilot to fly them, and learning to do so yourself is both tricky and expensive. Ask anyone who’s tried: crashing a several thousand dollar drone makes the learning curve steeper than the ascent to the summit of K2, and several thousands don’t buy you much in the way of farming tech. Wrecking a realistically expensive drone is like driving your car into a tree at highway speed--and just as painful to your wallet. As a result, a market for drone pilots servicing farms has emerged, allowing farmers to rent talent and equipment.
But that’s often not enough. The new agriculture is data intensive, and infrequent visits by drone pros can’t provide the precise, constant information farmers need.
In 2015, 3D Robotics introduced a solution that we think paves the way for the future. Their (then) $1,000 ‘Solo’ (now $244.98 on Amazon) dramatically improved the out-of-the-box usability of drones. The Solo has presets that allow it to follow the user automatically, training its camera or sensor on her. Moreover, by tracing a path on the screen of your phone, you can send the Solo on an autopiloted flight. Finally, by selecting coordinates or an object in GPS, you can tell the Solo to orbit, and it will slowly circle that point. In each case, the Solo flies itself and operates its camera.
Unless you’ve flown drones or know a lot about them, it can be easy to miss just how revolutionary this two-year old design is. Current, state-of-the-art agricultural drones often demand a team of two to operate: one pilot and one cameraperson.
3D Robotics’ Solo is the shape of things to come, and its easy to use interface and capable autopilot and camera controller were the first step toward real ‘unbox and fly’ tech. This is a trend we see a lot in technology: early efforts are clumsy, slowly being superseded by more elegant designs. For example, just a few decades ago, you had to know a programming language to operate a computer. Shortly thereafter, Apple and Microsoft began exploring better, more elegant, more user friendly ways to get computers to do what we need them to, eventually resulting in the touch screens and icon driven operating systems we take for granted on our phones and tablets.
We think something similar is developing in the world of drones, and we believe the future of drone tech in agriculture is automation. Imagine unboxing a drone, attaching a sensor package, and, with a GPS map of your field, selecting its boundaries. You throw the drone into the air and it surges upward over your crops. You watch, leaving the drone to figure out the most efficient route to cover the area.
SenseFly’s 'eBee Ag'
With drones like PrecisionHawk’s ‘Lancaster’ and SenseFly’s ‘eBee Ag,’ this is no longer something to think about in the future tense.
Both drones are offered as fixed-wing designs, and both need only be thrown into the air before they take control of themselves. Using your GPS maps and preselected options, they have the intelligence to fly themselves efficiently, deciding for themselves what path to take, how many passes to make, and what altitude is necessary for the best resolution. For about $25,000, these drones can survey your fields and provide real-time, actionable data.
That may sound expensive, but when you consider that renting a helicopter or plane to do the same job costs about $1,000 an hour, that price tag buys a lot of drone and not much helicopter rental. And as the cost of such advanced systems decreases (reconsider the dramatic decrease in the price of the Solo over just two years), we anticipate that automated drones will supplant their manual alternatives.
It’s Windows replacing DOS prompts all over again.
Swarm tech and helper drones
The real paradigm shift, however, will wait for swarm technology. Rather than a single smart drone that flies itself, imagine a future in which a legion of tiny drones makes use of ‘swarm intelligence’ to accomplish tasks with minimal direction.
Swarm intelligence is the problem-solving, adaptive, collective behaviour of decentralised, self-organised systems. In plain English, swarm intelligence takes advantage of the whole being more than the sum of its parts. Each drone isn’t that smart itself, but it makes use of a shared intelligence generated by clever algorithms. These formulae keep the drones apart, but not too far, and let the drones ‘think,’ ‘react,’ and ‘learn.’ In short, they enable the swarm to solve complex problems as a collective, problems no single smart drone could conquer.
Following the now familiar pattern of drone development, swarm tech will first be deployed by soldiers and airmen, only later finding its way into the hands of farmers. The US military is experimenting with swarm intelligence now, dropping a small army of tiny ‘Perdix’ drones from a pod mounted beneath an F/A-18 Super Hornet. As the drones right themselves in the wake of the jet’s wash, they self-organise and move to accomplish their mission--without really knowing how they’re going to do it.
They learn as they go, sensing, thinking, and adapting. As William Roper, the Director of the Strategic Capabilities Office at the Office of the Secretary of Defense, explained to MIT Technology Review:
Perdix are not pre-programmed synchronized individuals, they are a collective organism, sharing one distributed brain for decision-making and adapting to each other like swarms in nature. Because every Perdix communicates and collaborates with every other Perdix, the swarm has no leader and can gracefully adapt to drones entering or exiting the team.
As our understanding of what makes swarm intelligence tick improves, and as our grasp of the algorithms that empower it grows stronger, swarm tech will eventually push individual drones to the background. The possibilities for a swarm of tiny agriculture drones are simply too amazing for solo drones to compete. A swarm, for instance, could be told to look for pests, scatter across a field, and then cluster over the most profoundly affected areas, spraying precision doses of pesticide to kill the invaders.
This may sound far-fetched, but consider that DroneSeed, a company based in Seattle, Washington, has already received FAA approval to use drone swarms to deliver seed, water, and fertiliser in its reforestry efforts. They buy off-the-shelf drones with maximum payload capacities and flight times, and then modify them further, providing the advanced software that allows them to exercise their collective intelligence. These swarms are then sent into the woods where they act collectively to replant logged forests.
New drone “bees?”
Even that’s just the beginning. In the US, no farmer has ignored the rapid decline of the honey bee, and without these tireless insects pollinating crops, it’s hard to image a future for agriculture. Indeed, every year, they pollinate $15 billion of almonds, cherries, apples, and berries, helping farmers grow the foods we eat.
Their inexplicable deaths are threatening our ability to feed ourselves and the world. That has everyone worried. While we work to uncover the cause and find a solution, researchers and engineers aren’t sitting idly by.
For example, scientists in Japan accidently discovered a viscous goo that maintains its stickiness for years. By affixing horsehair to the underside of tiny drones (purchased from Amazon for about $100), and by coating this hair in their goo, Svetlana A. Chechetka, Yue Yu, Masayoshi Tange, and Eijiro Miyako soon demonstrated that these drone ‘bees’ could transfer pollen from the flowers of Lilium japonicum, the bamboo lilly. “With a bit of practice, the device could pick up 41% of the pollen available within three landings and successfully pollinated the flower in 53 out of 100 attempts,” explained Elizabeth Franklin, a researcher of social insects as Bournemouth University in the UK. Nevertheless, Franklin thinks these ‘robo-bees’ are poor replacements for the real thing, and Joe Traynor, a bee specialist, told MIT Technology Review, that “in California, the almond industry in that state alone requires 1.8 million hives—containing around 35 billion bees—to pollinate 900,000 acres of almond trees that sprout three trillion flowers.”
That sounds like an insurmountable problem. Experts worry that, beyond the colossal number of such drones that would be required, the obvious expense, and their poor current performance--to say nothing of the danger their rotors offer real bees--we don’t want to encourage the idea that we can replace vulnerable species with technological equivalents. Critics like Antonio Regalado see this experiment through the lens of their concern for our ailing environment, and that pushes them toward a degree of skepticism that’s unwarranted.
Their concern is certainly understandable, and we share their worry that we might see creatures as miraculous as honeybees as nothing more than biological tech. That’s not just repugnant; it’s dangerous.
But we believe it’s hard to find a farmer who doesn’t care about her land in the broader sense, hard to find a farmer for whom the environment is just a workplace. Farmers are stewards, and they know that if they don’t take care of the land (and everything that means), the land can’t take care of us. If we can’t save the bees, it’s unlikely that we can replace them. That notwithstanding, we believe we should encourage this experiment, if, for nothing else, because of what it can tell us about the possibilities of tiny drones for agriculture, tiny drones that, empowered by swarm intelligence, will soon be as essential to farming as the shovel, the horse, and the plough once were.
Drones may not replace the honeybee, but don’t bet on a future of agriculture that doesn’t increasingly depend on their capacity to reinvent 21st century farming.
Bibliography
- https://www.actiongear.co.za/blogs/reviews/introducing-the-precision-hawk-lancaster-5, accessed 25 July 2017.
- https://www.agritechtomorrow.com/article/2017/07/sentera-grows-high-precision-line-with-release-of-quad-sensor/10097/, accessed 25 July 2017.
- Condliffe, Jamie, “A 100-drone swarm, dropped from jets, plans its own moves,” MIT Technology Review, 10 Jan 2017, accessed 25 July 2017.
- http://dronebusinessmarketer.com/best-gps-drone/, accessed 25 July 2017.
- https://en.wikipedia.org/wiki/Normalized_Difference_Red_Edge_Index, accessed 25 July 2017.
- https://en.wikipedia.org/wiki/Normalized_Difference_Vegetation_Index, accessed 25 July 2017.
- https://en.wikipedia.org/wiki/Swarm_intelligence, accessed 25 July 2017.
- Franklin, Elizabeth, “Robot bees vs real bees – why tiny drones can’t compete with the real thing,” The Conversation, 9 Feb 2017, accessed 25 July 2017.
- Main, Douglas, “‘Drone bees’ are comically inept, expensive and dangerous to real bees,” Newsweek, 10 Feb 2017, accessed 25 July 2017.
- https://news.wsu.edu/2015/08/11/unmanned-helicopter-tested-for-rainwater-removal/, accessed 25 July 2017.
- Nicol, Will, “Automated agriculture: Can robots, drones, and AI save us from starvation?” Digital Trends, 2 June 2017, accessed 25 July 2017.
- Pierce, David, “The 3D Solo is one scary-smart drone,” Wired, 13 Apr 2105, accessed 25 July 2017.
- http://www.precisionhawk.com/lancaster, accessed 25 July 2017.
- Regalado, Antonio, “Watch this $100 drone try to do a bumblebee’s job,” MIT Technology Review, 9 Feb 2017, accessed 25 July 2017.
- https://www.sensefly.com/fileadmin/user_upload/sensefly/documents/brochures/eBee_Ag_en.pdf, accessed 25 July 2017.
- Van Vark, Caspar, “Drones set to give global farming a makeover,” The Guardian, 26 Dec 2015, accessed 25 July 2017.
About Richard van Hooijdonk
Trend watcher and futurist Richard van Hooijdonk began his career in the banking, publishing and technology industries. He held strategic advisory and management positions and sat on various Boards of Directors. Van Hooijdonk takes you to an inspiring future in which the way we live, work and do business changes dramatically. Van Hooijdonk's acclaimed inspirational sessions have already been attended by over 300,000 people. He is also a guest lecturer at various universities and works with RTL and BNR news radio where he presents his Mindshift program. Van Hooijdonk and his international research team investigate tech trends and their impact on various industries. He is author of numerous articles, publications and e-books, including Trends 2016. With an overall rating of 9.2, Richard van Hooijdonk is one of the most sought-after speakers in the Netherlands and abroad.
The content & opinions in this article are the author’s and do not necessarily represent the views of AgriTechTomorrow
Comments (0)
This post does not have any comments. Be the first to leave a comment below.
Featured Product
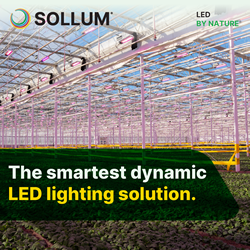