While crop producers lay out their best plans for success early in the season before planting begins, inevitably some combination of crop pests, unpredictable weather, and even the neighbors livestock or wildlife in the area can wreak havoc on those plans -- resulting in an accumulation of setbacks at harvest.
3 Ways to Reduce Grain Losses at Harvest Time
Jeff Keiser | Iteris
The period that approaches grain harvest each season poses many challenges and risks for farmers, with harvest-time losses estimated at 20% or more under adverse conditions. While crop producers lay out their best plans for success early in the season before planting begins, inevitably some combination of crop pests, unpredictable weather, and even the neighbor’s livestock or wildlife in the area can wreak havoc on those plans -- resulting in an accumulation of setbacks at harvest. In light of this, each harvest inevitably poses questions for farmers and their advisors, such as:
- Should I harvest my field early to avoid grain or plant stalks falling to the ground, making it harder to harvest and losing some of the crop on the ground?
- Will the grain in some of my fields hold moisture too long under humid conditions, resulting in grain contamination by molds or other pests -- causing my grain to be either un-sellable, or deeply discounted?
- Could I leave the crop in some of my fields longer, so that it dries down naturally and I can avoid the costs and hassles of drying grain in my storage bins -- or even avoiding additional grain price discounts when I sell?
While it’s common that once harvest begins farmers will work as long and as hard as necessary to bring in their crops and avoid harvest-time losses, but during the rush of this period it's easy to overlook the accumulation of grain drying costs or grain moisture price discounts until the farm accountant analyzes their business results, usually long after the combine and grain trucks have been cleaned up and stored in the shed for winter. If farmers and their trusted advisors had easy access to field-level grain moisture and a forecasted rate of grain moisture dry-down while the crop is still in the field, it would be possible to drive better harvest time strategies.
To reduce grain loss at harvest, and to optimize grain drying costs while improving crop margins, follow these three steps:
1. Harvest early to gain improved pricing for uncontracted grain
Target fields that have been affected by pests, or perhaps hail, to reduce crop loss due to stalk lodging. Early grain harvest field plans should also be prioritized based on the crop’s current grain moisture, as well as by the forecasted dry-down rate in each field over the next few weeks. In order to gather grain moisture information, traditionally the farmer would need to visit each field and hand-thresh out enough grain to measure with a grain-moisture tester. Now, this can be much easier through the use of field-level crop and weather modeling that delivers the same information, and is even better, since it is updated each hour of every day, which would be almost impossible to manage in the traditional fashion.
2. Optimize harvest equipment and staff logistics
Establish and optimize harvest equipment calibration settings early to avoid losing machine efficiency during rush harvest periods. Field crop harvestability and easier grain threshing can lower machine fuel expense by as much as 18%, according to research by John Deere, and enable increased field harvester speeds to save even more precious time. Operators should also monitor field grain temperature and moisture often to ensure safe grain moisture storage levels in the harvested grain. Since grain moisture levels and dry-down rates are highly correlated to localized weather and soil conditions, use a reliable source for this information, such as a trusted source of weather and crop modeling that accounts for the impacts of land surface and sub-surface impacts.
3. Save grain drying costs and minimize field grain loss
Evaluate daily grain moisture price discounts and artificial or mechanical drying expense cost calculations compared with in-field grain dry-down forecasts. This can be difficult to do since the values change often and may often come from multiple sources. Due to the growth of precision agriculture, farmers and consultants should also analyze grain moisture in each field, in addition to yield, across different crop management zones that are the basis for improved crop input plans (e.g. seed variety, fertilizer type & rate, planting date, etc.) for next season. Schedule artificial or mechanical drying operations when ambient air temperatures are higher, and relative humidity is lower in order to further reduce drying expense.
Whether a particular crop season is average, or grain production is a “bin buster,” each crop harvest season will be fraught with questions, despite farmers and their advisors often having a lot of good gut instinct about what to do in certain situations. The three strategies suggested here will help guide crop advisors and farmers to manage harvest-time expenses, while increasing combine and harvester efficiency, and will be easier and more accurate with field-level grain moisture data and a forecasted rate of grain moisture dry-down while the crop is still in the field.
About Jeff Keiser
Jeff Keiser is VP for the Ag & Weather Analytics Division at Iteris Inc., a global company in applied informatics for transportation and agriculture
The content & opinions in this article are the author’s and do not necessarily represent the views of AgriTechTomorrow
Comments (0)
This post does not have any comments. Be the first to leave a comment below.
Featured Product
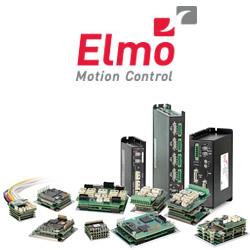