Telematics involves precision farming solutions by automating decisions or actions at a distance. The farmers “smart” machinery would apply seeds and fertilizer at variable rates based on the soil characteristics
Using Telematics in Farming
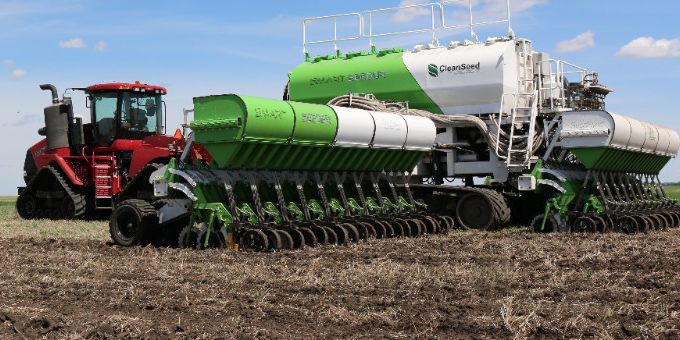
Len Calderone for | AgritechTomorrow
Telematics involves precision farming solutions by automating decisions or actions at a distance. The basic concept behind precision farming is that a farmer should not evenly apply seeds and fertilizer to their fields. Instead, a farm would be meticulously mapped using machinery with the proper soil sensors. Then, the farmer’s “smart” machinery would apply seeds and fertilizer at variable rates based on the soil characteristics, such as nitrogen levels, organic matter content, and moisture at various locations in the field.
There are a lot of sensors that are being used. As an example, there are twenty sensors on a seed spreader. These sensors measure not only the amount of seed that is being applied, but also the quality. If the quality is low, the machine in real-time will increase the amount of seed.
The machines can be manually or remotely controlled using devices such as an Xbox controller. A smart phone is used to launch autonomous operation. A guidance algorithm delivers ±2 cm accuracy. Speeds are precisely controlled and the automatic speed control makes safe turns. These smart machines can operate day or night with extended hours of continuous operation. Some machines have optional features, such as remotely accessible cameras, remote monitoring, diagnostic systems and weather stations.
The savings from variable seed application could be 15 percent and 19 percent for fertilizer. Overlap control, because of GPS-guided steering, saves 6 percent on seed because when the spreader comes to the end of a row and turns around, the turn is precise. Therefore, seed and fertilizer are never placed twice on the same land.
IoT and related technologies will transform a farm’s business model because data is collected by the sensors mounted on the GPS-equipped farm equipment. Big Data then uses the huge volume of data to create a digital platform. The farm’s machinery would connect to the platform, along with drones and satellites. The platform can be also be used to integrate with suppliers to improve the inbound supply chain. Farmers can share intelligence to reduce crop wastage from inefficient logistics.
Robots and autonomous super-tractors are part of the solution to make agriculture more efficient. Crammed with cameras and sensors, a metal crab works its way through a cornfield, sowing, fertilizing, and planting. Dozens of these intelligent robots are capable of working a complete field autonomously in one day.
The technology required to achieve variable rate fertilization includes an in-cab computer and software with a field zone application map, fertilizer equipment capable of changing rates during operation and a GPS system. Automatic section control technology turns seed planters off in areas that have been planted earlier, or on and off at headland turns, point rows, and waterways. This same technology is used with sprayers and fertilizer applicators.
Fields can be divided into management zones, which allows farmers to use different production techniques based on the distinctive conditions in each location. Fertilizer application maps indicate the amount of fertilizer needed for crop production in each zone and are used for variable-rate fertilization.
LiDAR (Light Detection and Ranging) is an optical remote sensing technology that measures the distance by illuminating the target with Light. LiDAR technology is used in airplanes to measure features on the Earth's surface, including detailed elevation. Using LiDAR data, the ground surface elevation contours is used to formulate both surface and subsurface field drainage patterns.
LiDAR can determine where to apply expensive fertilizer. It can create a topographical map of the fields and reveal slopes and sun exposure of the farm land. Researchers at the Agricultural Research Service uses this topographical data with a farm’s yield results from previous years, to determine zones of high, medium, or low yield.
Another application is crop mapping in orchards and vineyards to reveal foliage growth and the need for pruning or maintenance, and the variations in fruit production.
Optical crop sensors are used to gauge crop conditions during the growing season by directing light waves at crop leaves, and measuring the type and amount of light reflected back to the sensor. Green plants absorb much of the visible light wavelengths, particularly the blue and red-light waves, and they reflect a great deal of the green light waves. Plants absorb much less near-infrared (NIR) light than red light. Darker green leaves reflect more NIR light and absorb more red light than lighter green leaves. These reflectance characteristics of plants are used to develop vegetative indices to compare the relative health of crops.
Nitrogen losses has prompted growers to consider alternative management strategies that have the potential for improving crop nitrogen use efficiency. This involves the use of crop sensors to measure canopy nitrogen status.
The future of the technology lies in two machines in the same field knowing application coverage, no matter which machine covered it first. A grain cart operator can know the location and fullness of each combine bin and where it will be in the field when it gets full. Of course, there are robotic machines that talk to each other.
Getting to the future is going to require dependable wireless communication, new sensors on machines to collect the needed data with new and easy to understand in-cab displays while collecting the correct data.
The time spent driving down the road and between fields is underestimated, as well as the time to drive a tender vehicle to the sprayer to recharge the tank. The travel speeds are less than the driver thinks, and he often spends more time pushing buttons on the display than he realizes. Overlap is a problem because slowing down in the headland puts on extra coverage. Therefore, the telematics need to be analyzed and implemented in smart machines.
Farming equipment tends to be very big, very expensive and extremely heavy. That means that the operator can’t exactly stop at the local dealership if something goes wrong, and when it does it can be major, leaving the combine or whatever other vehicle in the middle of the field, unable to move under its own power. That’s why telematics are a lifesaver for many farmers, since the maintenance company or manufacturer can monitor the vehicle remotely, checking its systems and checking that the vehicle isn’t set to overload any stressed components.
Farmers now have the ability to remotely collect and manage information from their field equipment by using telematics technology. The future of farming is here today.
The content & opinions in this article are the author’s and do not necessarily represent the views of AgriTechTomorrow
Comments (0)
This post does not have any comments. Be the first to leave a comment below.
Featured Product
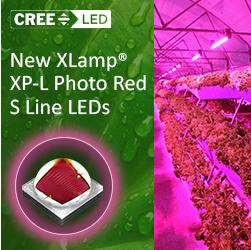