We call our hero BigTop, an autonomous, mobile robot with the ability to move 250 pots an hour and have a run time of 16 hours on interchangeable batteries.
The Age of Autonomy: Robotic Solutions for the Horticulture Industry
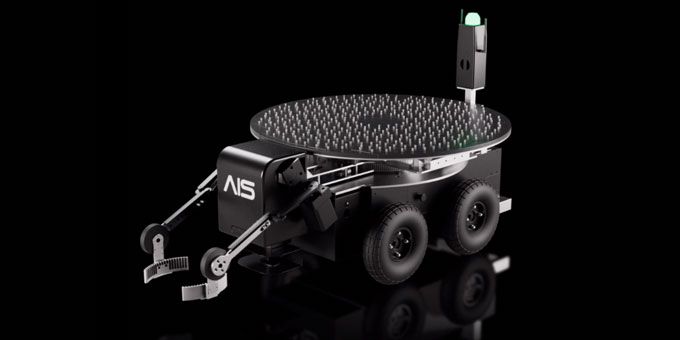
Afshin Doust | Advanced Intelligent Systems (AIS)
It’s hardly a secret: Every nursery and greenhouse operation has felt the pinch of chronic labor shortages. Finding and keeping people to perform repetitive, labor-intensive tasks has been a constant strain on the profit margins of the horticulture industry — and the backs of workers.
A lack of labor, combined with on-the-job injuries and inefficient processes that result in overuse of valuable water and fertilizer resources, are just some of the challenges that result from production issues. And the goal of meeting product demand gets pushed farther and farther down the line.
My company has developed a modern solution to an age-old challenge: Efficient, predictable and accurate autonomous robots that not only increase productivity, performance and worker satisfaction, but also save valuable and costly resources.
We call our hero BigTop, an autonomous, mobile robot with the ability to move 250 pots an hour and have a run time of 16 hours on interchangeable batteries. BigTop uses a set of sensors to observe its surroundings, enabling each robot to make autonomous decisions about its behavior or, if preferred, pass the information on to an operator.
BigTop’s parent is Advanced Intelligent Systems (AIS), a leading custom robotics company based in Burnaby, British Columbia, with the intellectual property to create affordable, autonomous, custom robotic solutions for any industry problem.
These intelligent robots can space pots to reduce water and fertilizer use. They can also move and rotate plants to aid growth and provide cost and environmental benefits.
BigTop uses two robotic arms to carry up to nine plants at a time. It places the plants securely on its rotating platform base, then travels to the new location and the robotic arms relocate the plants, spacing them in a pre-programmed pattern. BigTop is able to navigate and operate in both indoor and outdoor environments, reaching speeds of one meter per second, with a payload of up to 50 kilograms (roughly 100 pounds). And it’s on the job 24 hours a day, seven days a week.
The robot’s speed and accuracy outperforms manual labor by 50% and eliminates the obvious physical toll on workers. And when these robots are put to work, our research shows existing employees won’t be replaced, they’ll be applauding.
From the pilot study currently in place at one of British Columbia’s largest nursery operations, it is expected that job satisfaction will rise significantly as experienced workers will have the freedom to focus on more diverse and challenging tasks, cultivating a strong corporate culture and a work environment that supports this nursery’s values of respecting people and constantly searching for a better way.
When BigTop operates independently, its autonomous decision-making ability is based on pre-programmed algorithms that are designed to allow BigTop to perform the required job with simple instructions provided by the nursery. Flexibility is built into the artificial intelligence that allows the robot to operate independently. Or, it can be remotely controlled by an operator using feedback from the robot to operate.
In addition to plant moving and spacing, an add-on module has been developed for BigTop that can pick up, prune and replace the plant in its desired position. We’re also developing another artificial intelligence feature that will assess plant health by photographing its leaves and comparing that to a database of leaf images.
Rather than being saddled with an out-of-reach purchase price, companies rent the robots and pay for the work they perform.
This “Industry 4.0” technology leads to the obvious question: Is the autonomous robot part of the future of nursery and greenhouse cultivation? The horticulture industry employs 97,000 people in North America and Europe just to move pots, and with the injuries those employees suffer from constant heavy lifting, those positions are getting more difficult to fill. Autonomous robots seem likely to be a good solution.
And that’s good news for any emerging industry where the only thing that is constant, is change.
About Afshin Doust
Afshin Doust was appointed CEO of Advanced Intelligent Systems in 2016, with the goal of creating innovations in autonomous robotic solutions for a wide range of applications. He is a seasoned entrepreneur with professional experience in finance, sales, business consulting and strategic management with a keen interest in assembling teams to resolve business challenges. One of his favorite quotes: “I am still learning,” Michelangelo, age 87.
The content & opinions in this article are the author’s and do not necessarily represent the views of AgriTechTomorrow
Comments (0)
This post does not have any comments. Be the first to leave a comment below.
Featured Product
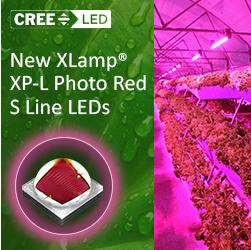