Automation can make a profound difference in the processes that are involved in getting food from the field to the grocery store, and onto the tables of millions of people. Automation can make a positive difference in food production, especially during the time of COVID-19.
Food Industry Automation: Improving Efficiency, Quality Control, and Traceability
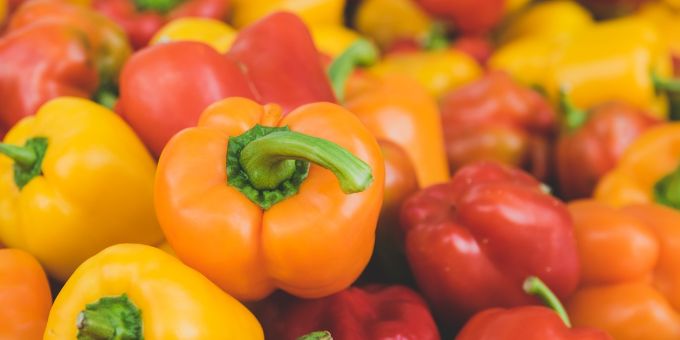
Article from | Jori Hamilton
For many leaders in the manufacturing realm, the idea of automation is a well-accepted one. There is almost no argument that it can be used to substantially improve the quality of business in a variety of ways including greater efficiencies, accuracies, and employee safety. However, when we are thinking of these advances, our minds are generally fixed in the realm of manufacturing things people use.
One of the realms that generally gets overlooked is food production. Yet, even here, automation can make a profound difference in the processes that are involved in getting food from the field to the grocery store, and ultimately onto the tables of millions of people. In fact, automation can make a real positive difference in food production, especially during the time of COVID-19.
These types of improvements come in many forms whether it is food safety, transparency, or even an increase in higher-level food production jobs.
Efficiency
An increase in efficiency is the cornerstone of choosing to automate a production process — this is no different in food production — money is saved when more is produced with less time or error. For instance, automation will increase production line flexibility. One way this has been happening is through modularization — which essentially means to break production into components arranged in a certain order. Newer ideas can replace individual modules without a complete slowdown in productivity.
Often, companies not only report that their bottom lines have increased but actually that their employee productivity has as well. Automation allows food production companies to get people out of the manual, repetitive positions and into those that require a little more technological background. To say that automation costs jobs doesn’t quite cover the whole story — manufacturing, in general, is experiencing growth in hiring people with general technical skills.
Automation of food production can also increase efficiencies by enabling companies to data mine — a process that is quickly becoming an integral part of business, marketing, and analytics. The huge amount of data that is collected in an automated system can help trace food origins and track where potential issues are coming up, allowing for better responsiveness to safety concerns or mechanical issues.
Quality
Automation can also do a great deal to improve the quality of the food products that are being put through the production line. Quality is a key factor for many food companies when it comes to competition. This is especially true for smaller companies that are working against some of the larger ones. Small increases in quality and consistency go a long way towards developing a loyal following.
Much of the food production industry is already preparing for greater automation and a reduction of human labor on the actual food line. Many are already using some sort of automation for packaging and plan to integrate more automation into other aspects shortly. It is recommended that introductions are made over time to reduce buy-in costs — as long as the new pieces can adequately integrate with older systems until all the newer pieces are in place.
When it comes to ensuring the quality of our food in the COVID-19 world, automation can also play an important role. For example, automation can help reduce the number of people who need to interact directly around food or within a space occupying a lot of other people. This can not only make food production safer, but it can protect employees from COVID while still achieving company production goals.
Traceability
In today’s world, there is a growing consciousness and concern for where exactly our food comes from. Was it produced locally, regionally, or halfway around the world? What practices went into producing these products and were they sustainable? Finally, if a food-borne illness is circulating, how do we know which general area or farm is responsible?
Automation can help with answering these questions as well. This is because automated food production chains have a greater ability to track where food comes from and whether or not there are certain risk factors to be aware of. This enables both producers and consumers to protect themselves from health risks and gives people a greater insight into the footprint their food consumption habits have.
Traceability also puts more of an onus upon producers to meet health and environmental regulations. Part of why this is so is because consumers can now research the exact farm their tomatoes are coming from and determine if they support the farming practices. Ultimately, traceability through automation can increase awareness and perhaps encourage people to make less impactful, more local food choices.
The content & opinions in this article are the author’s and do not necessarily represent the views of AgriTechTomorrow
Comments (0)
This post does not have any comments. Be the first to leave a comment below.
Featured Product
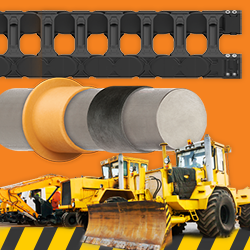