With so many variables and Mother Nature becoming more unpredictable, our horticultural experts continue to field an increasing number of enquiries for controlled growing environments.
What Is the Future of UK Vertical Farming?
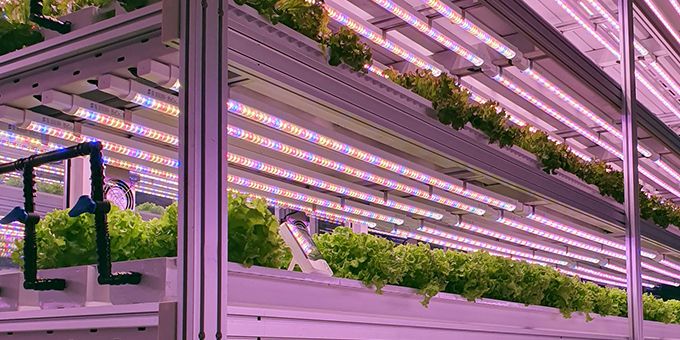
Tim Haworth, Head of Technical Horticulture | Cambridge HOK
Climate change is increasingly having an adverse impact on open-field farmers.
Some are finding conditions too wet or too dry. For others, it’s too windy, too cold or too hot.
With so many variables and Mother Nature becoming more unpredictable, our horticultural experts continue to field an increasing number of enquiries for controlled growing environments.
Step forward vertical farming.
Having built our first vertical farming facility in 2011, we believe this revolutionary growing system will form a key part of UK food production system for decades to come.
In our experience, growers want to produce same food to a high quality without using pesticides.
Vertical farming is a vehicle which can allow this to happen. All year round. No restrictions. No worries about adverse weather.
If growers can better predict their yield, they can start to plan ahead and develop their business model with more certainty. More time can then be spent working to develop a better-quality product with a better shelf life.
A new premium salad tier
Essentially, anything can be grown in a vertical farming space but there’s no point in doing so if it is not commercially viable. Consequently, what can be grown is driven mainly by what growers can sell – and how much they can get for it.
At the moment, vertical farming is predominantly focused on short grow crops which can be grown at volume in a vertical space. Higher-value herbs and leafy greens are the crop of choice because they deliver a better return for the money which has been spent to grow it.
Whilst we expect the future of UK vertical farming to be driven by commerciality, because of the need to be commercially viable, successful results (and profits) will impact on future growth and scalability.
Consequently, we believe vertical farming could create a new tier in the salad category – delivering a premium product which sits alongside traditional supply chains.
Bigger, better & automated facilities
To deliver a successful commercial vertical farm, we believe a minimum grow space of around 5,500sqm is required. It’s easy to design and build a much smaller-scale vertical farm, as we have in the past, but our analysis shows 5,500spm is the optimum size for commercial viability.
Neatly positioned inside a 4,500sqm building, including separate packing and back-office areas (based on growing five layers high), this type of facility can be developed modularly to gain economies of scale over time.
Given that a £10-15million capital investment is needed to build a 5,500sqm grow facility, vertical farming is only for retailers, growers and investors who are serious about the industry. To be successful on this scale, investors will also need to be serious about automation.
For the next generation of vertical farms to work efficiently and ensure consistent production, we believe automation is vital. Growers will not be able to manage the complexity and the number of movements required each day without it.
The amount of automation required is usually driven by the scale of the farm and the crop type being grown.
To achieve the optimum ROI, we work in partnership with SEC Automation to analyse the capital expenditure budget available and asses the level of profitability required from the facility. Moving forward, we believe this analysis will be vital when advising whether to opt for low, semi or full automation.
Detailed business plans & financial modelling
Since becoming involved in the initial vertical farming research process in 2011, we have designed and built 10 facilities around the world. From very small scale offering to large commercial vertical farms.
Before starting any project, we now provide every potential customer with a detailed business plan and robust financial model so they fully understand what could be achieved. They can then make an informed investment decision.
Whilst we are a pioneering technology provider, the in-house expertise we have means we can act as a one-stop shop for vertical farming. Rather than just design and build vertical grow systems, we help with all the other processes and considerations beyond that.
We think of the entire business – from germination to propagation, movement, climate control and grow systems to the packing areas and offices. We also provide the plant rooms and electrical infrastructure required.
The fact we understand how crops grow and the key environmental inputs required to improve quality and output places us in a unique position.
As the UK vertical farming industry evolves and grows, we think investors will see the value of gaining all of that expertise under one from a single contractor.
Beyond that, we anticipate increased interest directly from retailers as they bid to understand more about vertical farming and the benefits it can bring as part of their supply chain.
By Tim Haworth, Head of Technical Horticulture
Are you looking to invest in vertical farming?
Click now to learn more about our VF Concept – or call 01430 449440 and speak to our experts.
The content & opinions in this article are the author’s and do not necessarily represent the views of AgriTechTomorrow
Comments (0)
This post does not have any comments. Be the first to leave a comment below.
Featured Product
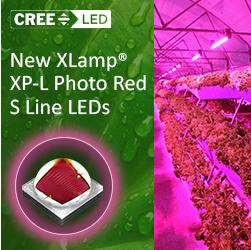