The 21st century has ushered in the era of commercial renewable energy. On each project, owners, end-users, developers, and subcontractors explore numerous options to maximize the efficiency of each plot of land.
Agriculture + Solar, the Perfect Pair for Modern Farming
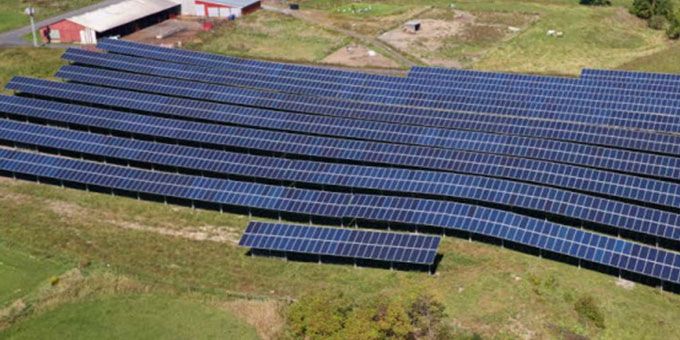
Case Study from | Terrasmart
Agrivoltaics — the dual use of land for both solar and agricultural production — offers the ultimate win-win. Through this symbiotic relationship, farmers and PV developers can work together to harvest planetary benefits. Solar sites are constructed in a way to coexist with existing cultivation practices, allowing farmers to maximize the production of their land. Agrivoltaics have been shown to increase crop production, protect ecosystems, reduce water use, and create a sustainable, more productive food system — all while generating income and saving farms.
This blossoming interest comes from the system’s ability to address climate concerns while simultaneously preserving farmland and meeting the growing demand for solar sites.
In fact, harvesting both food and energy from the same site can improve the land’s quality and increase crop production. Dual land use stabilizes finances for farmers, protects farms from future development, increases local property values, and generates local jobs.
PV panel shade can create higher crop yields, especially for fruits, according to studies by German research organization Fraunhofer ISE. Solar panels protect against hail, frost, and drought damage, eliminating the need for protective foils and other materials. By reducing wind and solar radiation, PV modules also can decrease water consumption up to 20 percent. In one case, potato crop land use efficiency rose 186% under PV panels.
Over the past decade, the Terrasmart team have developed and deployed adapted racking systems and customized wire solutions that allow growers to harvest the sun’s power twice, generating energy while simultaneously increasing crop yields.
Customized wiring provides berry benefits
Background
Local farmers in Southern Massachusetts looked to an agrivoltaic solution to capture and store solar energy over special cranberry wetland farms, otherwise known as cranberry bogs. The dual-purpose land use allowed for 9MW solar panels with 36MWH storage to be installed over fully functioning cranberry bogs. In doing so, the developer had to consider the complexity of dual-purpose lands. Installing solar panels over 150-year-old cranberry vines is an exercise in caution, requiring precise placement of panels and wiring. The arrays must be high enough to ensure minimal damage to the crops below and allow for farming activities like harvesting to take place seamlessly. This level of complexity cannot be addressed by generic, off-the-shelf wire solutions. The customer needed a partner that could problem solve for them and deliver within a short lead time to ensure installation could occur alongside the racking and panel installation.
Challenge
In building the agrivoltaic project, the developer needed to ensure that the arrays would have solid foundations, durable racking structures, and be placed at an atypical height to minimize impact on crop growth and harvest activities. The accompanying wiring solution also had to conform to these specific conditions. Specifically, the wiring solution deployed needed to fulfil three key conditions in the overall project:
The solar arrays had to be mounted on 25 to 40-foot-long wooden, wet terrain-resistant utility poles. These poles were also driven 15 to 30 feet into the ground, keeping the trackers at least 10 feet above the cranberry bogs. At this height, significantly more wire is required as compared to average solar projects.
Keeping the cranberry bogs fully functioning and undisrupted was key, and the wiring solution needed to be one that would minimize long and heavy in-field installation activities.
The lead time and project turn time were very short. The project needed to be delivered within a tight 6-week timeline, a challenge when considering the average timelines for wire projects are 8 to 12 weeks.
Solution
Given the short lead time, the team was all hands-on deck reviewing production schedules, drawings, and site plans to support the end-goal of ensuring the most optimized wiring solution for the project—one that was customized for fixed conditions and variables: height, placement, quantity, human activity, and project turn times. Instead of waiting for racking to be completed before installing the wiring, the solution was coordinated alongside the racking and module installations to minimize any disruption to harvesting.
The wiring was factory-assembled to ensure quick installation in the field. A total of 1,384 source circuit conductors (half positive, half negative) were cut to length and labelled in the factory with MC4 connectors installed on the panel end. It was blunt cut on the opposite end for easy field connection to Terrasmart combiners. The end-to-end connectivity of the wiring solution and shipping on spools allowed for quick plug-and-play in the field. Having the wire prefabricated ensured faster and quality results during installation.
Result
By leveraging Terrasmart’s team of experts, the complexities of the project were addressed and absorbed, upfront allowing for no disruptions during harvesting.
The outcomes of this project include:
1. Customized wiring that accommodated the atypical heights of the agrivoltaic projects, providing consistent and accurate cut lengths.
2. Ease of wiring integration with already purchased combiner boxes.
3. Creative problemsolving upfront to deliver solar to more fields, no matter how complex.
4. A wiring solution that was delivered in coordination with other aspects of installation on site such as racking and modules, shaving weeks off the typical timeline for a project of this size and complexity.
5. Customized prefabricated wiring provided a solution where off-the-shelf, bulk wiring was not an option due to the unique cranberry bogs.
6. The project was delivered within a tight timeline, ensuring the build-out will not affect the cranberry harvest.
Solar grazing proves to be a win-win for farmers
Though produce farms remain the majority in agrivoltaics, the prospect of livestock farms has increased in recent years. Fundamentally, the practice is the same, but livestock farm projects require more robust engineering to ensure the safety of the animals grazing below the structure.
In 2013, the state of Vermont set a goal to reach 90% clean energy by the year 2050. To help achieve that goal, the Vermont Agency of Agriculture, Food, & Markets championed policies to pair renewable energy and farming. State tax policies allowed for farmers, who added renewable energy resources, to gain a tax subsidy from the renewable energy project along with the subsidy from their agricultural production.
The economics of farming can vary based on the agricultural output year to year. By pairing agricultural farms with solar, farmers can add a second source of revenue to their business with a more predictable revenue stream.
The owner of Maple Ridge Meats in Benson, VT looked to utilize the benefits of agrivoltaics at their 650-acre livestock farm. The farm chose to lease a 5-acre plot where cattle grazed every day to a solar developer who would convert those acres into a 500-kW solar site.
Challenge
One condition for Maple Ridge Meats was to ensure agricultural production could still take place and that cattle could still graze on site. This meant designing and engineering a taller racking system for the solar modules to sit on. The taller height would ensure the grazing cattle would not touch the modules. The team also had to take into consideration that cattle would be bumping into the racking structure while grazing. This meant they needed to design a solution that would be more structurally sound than your typical racking system.
As with all solar projects, the first step in designing a solar site was to understand the underground soil conditions. Since the racking system was going to be built several feet higher than a typical fixed-tilt system, foundation design was going to be critical in getting the project to pencil. Typical fixed-tilt systems in Vermont may see a clearance height of 30-36 inches from the front edge of the module to the ground. The Maple Ridge Meats project would require that clearance height to more than double, up to 7.5 feet to ensure safe grazing.
Solution
The Terrasmart field team conducted on-site pile load testing during the early design phase of the project. At this point, our engineers determined we could drive posts into the ground for the foundations. Instead of a standard W6x9 post, this project was engineered with longer W6x12 posts. The larger sizes were utilized to support the taller height of the structure and to accommodate the heavy 40psf snow loads of Vermont.
To provide more stability for grazing cattle, engineering decided that the posts should be driven deeper than the typical post. This is similar to how we design canopies, as they must be engineered to withstand vehicles bumping into the columns. Cowport, the name we gave this unique racking design, required posts to be embedded 12 feet into the ground, 5 feet deeper than the typical posts found in Vermont. Our team utilized our proprietary post driving machines that can install posts up to 24 feet in length.
The taller height of the racking required the installation team to take a different approach. Jeff Cooley, Terrasmart Project Manager, noted “it was tricky because we typically use 4–6-foot ladders to complete installation. However, on this project, we had to utilize a four-wheel drive scissor lift due to the taller height. Installation took place in the spring, so we utilized matting under the lift to ensure safety of our field team.”
Result
While some people may not think farming and solar development are compatible, given in the past they have competed for land. This project shows how these partnerships can be mutually beneficial. This outcome was a win-win for both parties by diversifying income for the farm while also working to meet Vermont’s clean energy goal. The raised arrays provided comfort for the cows, giving them shelter from both sun and rain without impacting the agricultural production. By choosing to partner rather than compete, farmers and energy producers can plant an innovative path forward for solar development and farming.
The content & opinions in this article are the author’s and do not necessarily represent the views of AgriTechTomorrow
Comments (0)
This post does not have any comments. Be the first to leave a comment below.
Featured Product
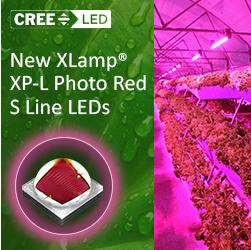