Predominantly known for their automatic bagging equipment, Haley recently introduced the industry's first-known robotic pad inserter. The 6-axis robot places cardboard top pads in different-sized produce boxes.
Robotic Evolution In Packaging Automation Delivers Greater Efficiency
Case Study from | Mitsubishi Electric Automation, Inc.
An Industry That's Ripe for the Benefits of Robotics
The need for more and more automation in produce packaging has grown, as people are becoming scarce and packaging types and materials are changing constantly. Haley Manufacturing is at the forefront of innovation with high-tech automated packaging machines for everything from bagging to boxing produce. Their automated packing systems will help produce packagers lower their costs and increase volumes, while reducing reliance on hard-to-find labor.
Predominantly known for their automatic bagging equipment, Haley recently introduced the industry's first-known robotic pad inserter. The 6-axis robot places cardboard top pads in different-sized produce boxes. As boxes move down a conveyor, the robotic system determines the box size and picks the appropriate pad for each box. Haley Manufacturing's latest packaging automation innovation is a robotic pad inserter.
Working with the pad manufacturer and Mitsubishi Electric Automation, Haley engineered the robotic pad inserter. When asked why robotics and why now, Brandon Haley, Co-owner and President of Haley Manufacturing, said, "This was our first use of a robotic arm. There was definitely some concern, but it just made sense for the application and for our future. We didn't want to do what others in the industry had done. We wanted to create our own foothold on the market."
According to Jeremy Briskey, Service Manager at Haley, "A pretty good percentage of the market still handles pad insertion manually. Some OEMs offer mechanically-automated pad insertion systems for foam pads and other materials. These systems require a larger footprint, have reliability and accuracy issues, and are limited to one pad size. Also, the industry as a whole is getting away from foam pads because they can't be recycled."
Gil Ansart, Sr. Sales Engineer at Mitsubishi Electric Automation, said Haley's primary goal in designing the robotic pad inserter was keeping the labor rate down. That meant the pad dispenser had to have the capacity to hold a large volume of pads, so operators could load it and forget it. Haley also wanted the robotic pad inserter to be able to accommodate different sizes and types of pads.
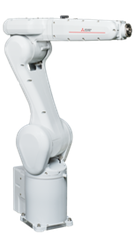
Built for Business Agility
- Less CAPEX up front
- Better throughput and ROI
- Increased reliability and accuracy
- Built-in business agility
Brandon says, "It's not just flexible for today. It's adaptable for tomorrow too. The system currently supports two different pads. If and when it becomes necessary to run even more pad sizes, all you have to do is add another pad magazine."
Murpack provides the robotic pad inserter to end customers who purchase their pads. They say it's significantly more reliable than mechanical inserters because robotics are driving the system. As a Diamond Partner OEM, Haley Manufacturing receives valuable engineering, manufacturing and marketing assistance from Mitsubishi Electric Automation.
A Lot of Perks Working with Mitsubishi Electric Automation
Haley is an automation-centric company, so it's no surprise they've worked with Mitsubishi Electric Automation since they introduced their first automated system. When asked about the six-year relationship, Jeremy says, "Our relationship has always been great. The technical staff and training has definitely helped us in a lot of ways and not just with robotics, but with PLC programming and HMI as well. And Gil is a great rep."
Haley Manufacturing is a Diamond Partner OEM, so they were able to try out the robot before purchasing it. They also received software and marketing assistance — all for being a member of the program. Haley plans on taking advantage of in-class training. Jeremy says, "There's definitely a lot of perks to it. We never missed a ship date all through COVID. Mitsubishi Electric Automation always got components to us on time or darned close. They're also a great knowledge source for us."
When asked about future plans, Brandon says, "We plan on continuing to grow, so the more automated equipment we can bring to market, the better. We really think the future is with robotics."
Learn more about Haley Manufacturing: www.haleymfg.com
The content & opinions in this article are the author’s and do not necessarily represent the views of AgriTechTomorrow
Comments (0)
This post does not have any comments. Be the first to leave a comment below.
Featured Product
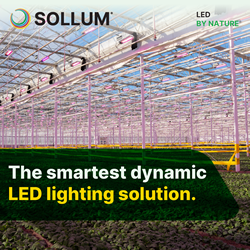