Despite being shielded from external weather conditions, indoor farms are not immune to the temperature and humidity challenges that accompany winter’s frosty arrival.
Is Your Vertical Farm Ready for ‘Old Man Winter’?
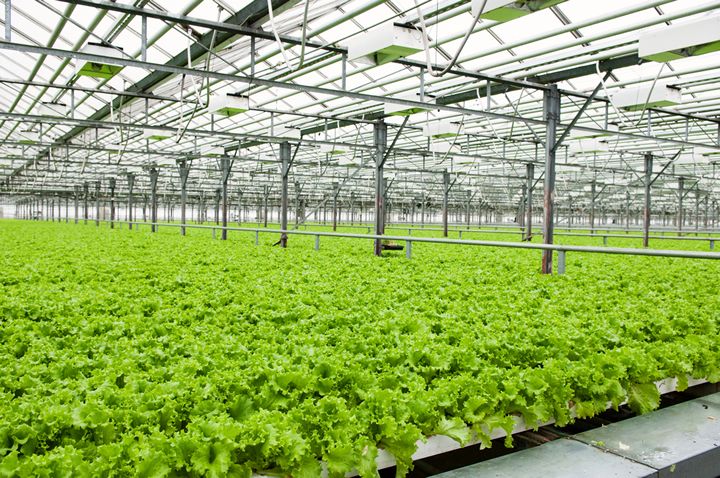
Jamie Tuinstra, Regional Sales Manager | Modine Manufacturing
As consumers continue to pursue fresh produce year-round, the demand for table-ready crops has skyrocketed. To meet this need, many farmers have turned to controlled-environment agriculture (CEA), which allows them to harvest crops indoors year-round and reduces their reliance on specific growing seasons.
As farmers aim to do more with less, vertical farming — an innovative CEA approach that involves growing crops in vertically stacked layers or structures — is booming. According to Statista, the vertical farming market topped $5.6 billion in 2022 and is expected to soar to $35 billion by 2032 — a 700% increase in just 10 years.
Vertical Farming Heating Solutions
Despite being shielded from external weather conditions, indoor farms are not immune to the temperature and humidity challenges that accompany winter’s frosty arrival. Condensation, temperature fluctuations and the need for efficient heating to keep crops thriving are crucially important during the cold season.
While specific indoor temperatures will vary depending on the crop, the need for added warmth in the winter months is necessary for proper photosynthesis, nutrient uptake, and growth. Temperatures that fall outside of the acceptable range may place undue stress on plants, potentially inhibiting germination, leading to stunted growth, a lesser yield or even death. Taking the right steps to prepare vertical farming operations is essential to ensure crops continue growing optimally at all times.
Compact unit heaters, which are available in many sizes and configurations, serve as formidable solutions for vertical farms. Additionally, these units’ ability to direct combustion fumes outside and away from the growing facility promotes clean and safe growing environments, making them ideal for indoor agricultural operations. Whether it's power-vented gas-fired units, separated combustion and power-vented units, etc., there is a unit heater solution available for nearly every indoor farming comfort need.
Electric Heating Solutions
Depending on your application and limitations, electric heating solutions may be easier to install than their gas-fired counterparts. Additional benefits include precise temperature control, space efficiency, and minimal maintenance. Offered in several sizes with inputs ranging from 10,200-133,100 Btu/hr, electric heating units are designed with long heat throw, uniform heat delivery, and reduced maintenance in mind. These compact and versatile options aim to optimize space without combustion, providing farmers with efficient and easy-to-install solutions where other fuel systems may introduce more complexities.
Radiant Heating Solutions
Radiant heating allows farmers to target specific zones, including plants and soil, directly. These solutions are designed to provide instant heat, making them ideal for spaces requiring quick warmth without waiting for traditional heaters to circulate air. They are available in gas-fired and electric configurations, in both radiant and infrared models, with inputs generally ranging from 1,500-200,000 Btu/hr.
Steam/Hot Water Solutions
Water is a crucial element in any crop’s life cycle, and, accordingly, farming operations tend to use an abundance of water. Building operators may consider using steam or hot water heating equipment in their farms, as hydronic solutions provide consistent and uniform heat across growing areas and minimize any fluctuations that could detrimentally impact crops. Steam/hot water unit heaters are offered in horizontal and vertical models with inputs generally ranging from 11,900-340,000 Btu/hr, delivering heat that can be delivered efficiently through zoned areas and ensuring specific segments of the farm receive heat at precise times and intervals.
Hydronic heating solutions also allow operators to precisely control humidity levels, minimizing condensation issues, which can lead to mold or mildew problems that can cripple indoor growing environments.
Building Management Systems
Building management systems (BMS) offer operations managers centralized platforms to oversee and regulate entire vertical farms, including their heating solutions.
In addition to controlling and monitoring on/off cycles from a centralized place, administrators can detect if one of their systems goes down in real-time, allowing them to immediately address the situation and avoid interruptions. Using BMS, farmers can collect data and analyze system performance over time.
Some unit heaters are equipped with BMS integration capabilities, allowing them to be added to existing BMS quickly and easily.
Seasonal Maintenance
Even with advanced HVAC systems and heating equipment, regular preventive maintenance is essential for sustained efficiency and equipment longevity. Without proper care, heating systems may malfunction, leading to inconsistent temperatures that can negatively affect plant growth, reduce yields or even result in crop loss.
Establishing a routine maintenance plan with licensed technicians helps avoid such risks, extends the life of the equipment and reduces energy consumption. For electric heating systems, this typically involves inspecting and cleaning heating elements and reflectors to prevent the buildup of dust and debris that could obstruct heat distribution. Technicians also check for loose connections or worn components that may lead to malfunctions. In gas-powered units, maintenance involves cleaning burners, inspecting vent pipes for rust or blockages and checking for any cracks or corrosion that could impact performance. Integrating these maintenance practices further enhances the stability and sustainability of the entire farming operation.
Winter Is Coming: Is Your Farm Prepared?
Vertical farms require a lofty investment, as startup, scaling, infrastructure and labor aren’t cheap. And, amidst these expenses, none carry a higher price tag than the energy required to keep such facilities operating comfortably and optimally. According to the 2021 Global CEA Census Report, vertical farms have a significantly higher average energy cost of 38.8 kWh per kg of produce compared to traditional greenhouses, which average 5.4 kWh per kg.
The success of your farm lies in implementing and maintaining a balanced environment where temperature, humidity and airflow are consistently regulated and prioritized. Implementing the proper heating strategy validates optimal plant growth and maximizes crop yields year-round. Ensure your farm operates efficiently and sustainably throughout winter’s deep freeze by administering the proper heating solutions and integrating them with comprehensive environmental controls.
Jamie Tuinstra is a regional sales manager at Modine Manufacturing. He has been in the heating and cooling industry for 25 years and with Modine for 16. At Modine, we are engineering a cleaner, healthier world. Building on more than 100 years of excellence in thermal management, we provide trusted systems and solutions that improve air quality and conserve natural resources. More than 11,000 employees are at work in every corner of the globe, delivering the solutions our customers need, where they need them. Our Climate Solutions and Performance Technologies segments support our purpose by improving air quality, reducing energy and water consumption, lowering harmful emissions and enabling cleaner running vehicles and environmentally-friendly refrigerants. Modine is a global company headquartered in Racine, Wisconsin (USA), with operations in North America, South America, Europe and Asia. For more information about Modine, visit www.modinehvac.com.
The content & opinions in this article are the author’s and do not necessarily represent the views of AgriTechTomorrow
Comments (0)
This post does not have any comments. Be the first to leave a comment below.
Featured Product
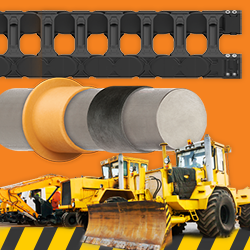