Small Robot Helps Space Plants for Greenhouses and Nurseries.
There are many examples of how tech has changed agriculture in an effort to improve efficiency. Crop and livestock genetic management, improved facilities that use sensor technology and wireless IoT data transfer, as well as increasingly specialized business models that invest only in the equipment, skills, and specialized tech to ‘do one thing and do it well’ are changes that have occurred and continue to develop within the industry.
Ag businesses have also increasingly relied on AI and robots to help perform certain necessary tasks. These robots are typically specialized and designed for one kind of job. One example of this is Harvest Automation’s container-moving robot. Weighing in at just about one hundred pounds, the not-quite two foot tall robot is designed specifically for use in greenhouse and nursery environments and is used to properly space out container plants.
The HV-100, also known as “Harvey,” requires zero programming and minimal training or setup. The robot uses sensor technology to identify containers, which it then grasps with its robotic arms. It then follows a pre-set guideline created from reflected tape (provided by the manufacturer) to carry the plant to the proper location. The unit will place each pot according to a specified pattern. The robot continues to locate plants and deposit them according to this pattern at a peak rate of 240 pots/hour until the job is completed or until removed from the job.
The HV-100 is designed for use in typical nursery and greenhouse environments. It can handle rain, dust, and dirt, and has a battery run-time of four to six hours. The robot is designed to pause if it detects a human being in its path. With battery swaps, the robots can continue with tasks on a near-continual basis.
While Harvest Automation’s HV-100 isn’t particularly high-tech--it’s more like Wall-E than a Blade Runner replicant, certainly--the units solve multiple challenges for medium and large nursery and greenhouse operations. They will do tedious, back-breaking work when it needs to be done, without the need for overtime, extra hiring, the risk of injury to workers, or the risk the job won’t get done. This also allows smaller year-round staff to successfully handle the necessary rotation of plants without the need to hire seasonal temporary help.
While the cost of each HV-100 is significant, typical payback for one unit when factoring in lower labor costs, improved production costs, and increased productivity is less than two years.
Technology writer Marla Keene works for AX Control Inc., an industrial automation supplier located in North Carolina.
Comments (0)
This post does not have any comments. Be the first to leave a comment below.
Featured Product
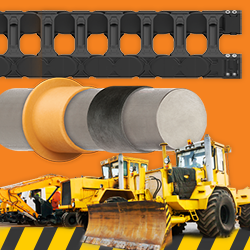