Trends in robotics: Cobots, agribots and medical robots
From recreational robots such as drones, to critical operational robots in the medical field, robotic technology is changing our daily lives. Here Stewart Goulding, managing director at precision drive system supplier Electro Mechanical Systems Ltd, explores some current trends in the industry.
Robots are everywhere — from robotic wearables, hands, and arms, to companion robots, medical devices, and even biomorphic drones that model the behaviour of bees. Main developments in the industry include cobots, drones and medical robots.
Cobots in the workplace
Since arriving on the scene in the mid-2010s cobots, or collaborative robots, have taken the market by storm. Cobots offer a variety of opportunities for production lines, particularly to enable humans and robots to complement each other, all while working alongside one another safely. The new trend for these styles of robots is making them more accessible, with more cost-effective options now allowing for greater distribution and use.
However, this is not the only way in which robots are collaborating with workers on the production line. Exoskeletons are mechanical devices that assist workers with uniform movements, support workers when lifting heavy objects, as well as providing a portable seat, helping to prevent strain on the worker’s body.
These applications are both improving the strength of production lines while reducing the strain on human workers and as cobots, exoskeletons and future forms become commonplace, the benefits they will grant workers, production process and businesses will become even more apparent.
In fact, cobots can reduce the human input on production by up to 50 per cent. With the current skills gap having cost UK organisations billions, being able to integrate cobots and other robotic applications, has the potential to positively impact the economy.
Medical robots
In recent years, a significant focus has been placed on revolutionising non-invasive and minimally invasive surgery. As a result, a deluge of new surgical robots have become market-ready. For example, the i-Snake® and Micro-IGES are both delicate robotic alternatives to traditional surgery.
Due to more accurate diagnosis methods, the amount of non-invasive and minimally invasive surgeries has skyrocketed. This is putting an increasing strain, both physically and organisationally, on surgeons that carry out these procedures. Robot alternatives, therefore, offer an advantage to the public health service.
As such, these robots must be as accurate and reliable as possible to ensure that they can help ease the strain on the medical system. For example, endoscopy, which is a minimally invasive surgery that allows doctors to inspect the inside of a patient, is one procedure that robots have been developed to support.
Endoscopy robots must be compact and consistently precise. For this reason, when French company EndoControl was developing its new endoscopy ViKY system, it chose a range of FAULHABER brushless DC-motors, which help to achieve the required precision and consistency.
With a complimentary gearhead fitted these motors have a broad selection of reduction ratios available ranging from approximately 3:1 to 1500:1, which gives extensive adjustment of the speed and torque of the device. In the ViKY systems up to 700 mNm of precise movement was achieved using FAULHABER drive systems.
These types of developments are crucial in ensuring medical facilities can cope with the rising number of surgeries, all while reducing fatigue, preserving surgeon wellbeing and avoiding burn out.
Robotics in agriculture
It’s no wonder that more agricultural robotic applications are emerging, including biomorphic drones that model the behaviour of bees. Robots and drones could have a big effect on the effectiveness of farming. From drones that monitor and analyse crops, to automated tractors that can seed, fertilise and harvest, agricultural robot developments all mean that human labour can often now be devoted to more complex tasks.
These applications require precise actuation in order to raise the efficacy of the systems. Drone cameras need smooth tilt and panning motion to ensure that accurate and usable images are taken to help. FAULHABER ironless rotor DC motors are widely used in moving camera applications, including defence reconnaissance and movie or television filming, as they allow for accurate cogging free movements to capture vital information.
Therefore, cameras for agricultural drones and other agricultural monitoring systems is a natural extension for this style of motor. Though drones may be considered recreational toys, their ability to autonomously cover and observe large areas of land in small amounts of time, all while consuming less fuel, is immensely beneficial to reducing operational costs.
In fact, some rural farms in China are starting to use heavy-duty industrial drones to water crops in hard to reach areas. The method is proving to be more fuel-efficient than transporting workers and the computer-controlled sprayers waste fewer resources.
So, whether it's across production lines, in surgical theatres or across vast agricultural fields, robotic applications are helping to provide innovative and reliable methods of working for all involved.
Comments (0)
This post does not have any comments. Be the first to leave a comment below.
Featured Product
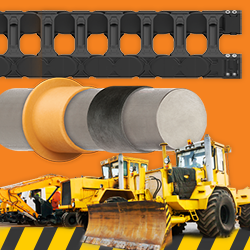