Selecting the Correct Material for Spray Nozzles: 8 Modern Options
When spraying pesticides or other chemicals on agricultural land, one of the most important decisions a farmer can make is the nozzle selection. There are a variety of nozzles available, but depending on the material sprayed, one could be more efficient and effective than another.
The type of nozzle used affects both the amount of material applied to a particular area and how uniform the overall spray is, the amount of coverage, and the drift that could occur due to the nozzle. Every nozzle is unique and has a specific application technique that works best for a given substance.
While the type and shape of the nozzle can affect the effectiveness and application of the chemical or substance, the material of the nozzle can also play a significant role in how well the nozzle holds up over multiple uses and a variety of sprays. Choosing the correct material for spray nozzles is something every farmer should consider when purchasing a new nozzle.
Types of Materials Used for Spray Nozzles
There are many different materials used for spray nozzles. From stainless steel to plastic, there’s a variety of options to make spraying fields the most efficient process it can be. The correct material can save a farmer both time and money. Below are some of the most commonly used materials for spray nozzles in the agricultural industry.
1. Aluminum
Aluminum nozzles are great for various gardening, lawn, and turf applications. However, since this is a softer metal, they aren’t the best for overall durability. They can wear a bit more quickly than other nozzles made of poly materials, stainless steel, or ceramic. Still, aluminum spray nozzles can be a dependable option.
2. Brass
Brass spray nozzles are generally robust and weatherproof. This material used to dominate before plastic became available because of its affordability and looks. Brass nozzles over 10 years old still hold up well as long as they’re taken care of. It’s resistant to corrosion and can withstand temperature extremes. However, they still wear a bit more easily than ceramic or stainless steel.
3. Hardened Stainless Steel
Spray nozzles made with hardened stainless steel are the most common for industrial sprayers. Hardened stainless steel is the most economically sound material for more extensive application needs. Even though they’re more expensive, they last through multiple sprays per year for generations. Plus, they generate a more uniform pattern for spraying over a longer time. If a farmer cannot afford hardened stainless steel nozzles, choose inserts with a nylon outer nozzle.
4. Stainless Steel
Stainless steel is a bit different from hardened stainless steel. Stainless steel has a lower carbon content, so it cannot go through the same heat treatment process as hardened steel. This makes it slightly weaker than hardened, but it is still a great investment for spray nozzles because it doesn’t rust or corrode. If spraying at a higher rate and volume, stainless steel is the way to go. Stainless steel is a popular option among farmers.
5. Polypropylene
Polypropylene is a type of plastic. It’s a more affordable option than most other spray nozzles, but that doesn’t take away from its durability. For the most part, plastic nozzles can hold up just as well as stainless steel. The process to make the nozzles is cheaper, and that makes the material more readily available. Another benefit is that these nozzles can be color-coded, which can be a time-saver when in the field. Farmers can check that the color matches the boom.
6. Combination Ceramic and Stainless Steel
Ceramic nozzles are another great investment for farmers who spray larger regions or amounts of product. Farmers who spray more frequently at higher pressures will want to get a combination ceramic nozzle with a stainless steel insert. These have a higher resistance and will last for years. They’re not used as frequently because they’re higher priced and have a stigma that they’re fragile. However, if they’re cleaned properly, they will last a long time.
7. Cast Iron
Cast iron nozzles aren’t as popular as other spray nozzles, but they still do the job. Cast iron is most widely known for its appearance in cooking appliances, so that means that it can withstand higher temperatures and won’t break under pressure. However, it isn’t a material that is resistant to corrosion. Any scrapes or scratches in the nozzle can spread across the entire surface in no time. Cast iron takes a bit more care and caution than other materials.
8. Nickel-Based Alloys
Nickel-based materials are another option for spray nozzles. They’re more resistant to corrosion compared to cast iron, brass, and some stainless steel. Nickel alloys have an extremely high temperature tolerance, which can withstand the hottest of days or spray products. Additionally, they have increased durability and reduce spatter when a pesticide or chemical is applied to a field, making the flow rate more consistent.
Factors to Consider When Choosing the Material
Before choosing a material for a spray nozzle, it’s important to consider the application process and substance being applied. Some sprays are harsher than others and can cause corrosion in no time, which wastes money spent on the incorrect spray nozzle material.
It can be challenging to know which material to choose for a spray nozzle, which is why there are various factors to consider when selecting a spray nozzle material. Here are some of those:
1. Frequency of Use
Spraying less than 100 acres a few times every year would only require a nozzle made out of a soft metal material. This low usage won’t put on wear and tear, and the nozzle can last for years. However, spraying more frequently requires materials that can hold up to the amount of spraying at high pressures. The materials best for high-frequency applications include polypropylene, stainless steel, and ceramic.
2. Temperature
Each type of nozzle material may soften if the temperature begins to rise. For farmers working in higher temperatures, the best materials include brass, stainless steel, and ceramic. Each of these can handle higher temperatures.
3. Abrasiveness
Farmers widely use spray nozzles to spread chemicals and pesticides. The material should be able to withstand the chemical. Ceramics and carbides are highly resistant to abrasion. Materials on the lower end of abrasion resistance include brass, aluminum, and steel.
4. Corrosion Resistance
Plastics are an excellent choice for corrosion resistance. However, they have a low temperature rating. The most resistant materials for corrosion are refractory metals and precious metals. Ceramics are also highly resistant to corrosion unless they’re in a high-pH environment.
5. Cost Savings
Budget is a consideration when choosing the correct material for spray nozzles. A nozzle made with ceramic or stainless steel may cost more upfront, but it may reduce overall costs also, since it won’t have to be replaced as often. Plastic, brass, and cast iron are a bit more affordable, but they could wear down faster.
6. Cleaning Requirements
Cleaning nozzles can reduce wear and tear, meaning it will last longer. Most of the materials for spray nozzles need to be cleaned with clean water. Water contaminated with fine particles can cause extra friction. After each use, be sure to care for the nozzles.
Material Matters When Choosing a Spray Nozzle
Be sure to choose the right material for agricultural spray applications. It can make all the difference in effectiveness, efficiency, and durability on the farm.
Comments (0)
This post does not have any comments. Be the first to leave a comment below.
Featured Product
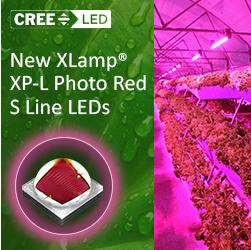