How To Optimize Weekly Maintenance Schedules For Agricultural Equipment
Humans have been engaging in agriculture for thousands of years. The ability to grow food diminished the need for foraging for human ancestors. Agriculture helped humans settle in one place and build civilizations. All major cities developed along river banks due to this fact.
Over the years, farming has gone through many changes due to technological advancements. From the use of the plough, technology made farming simpler and more efficient. Modern farms of this age use many complex machinery and equipment to make farming effortless. It helped farms to rely less on human labor and improved productivity dramatically.
The share of people employed in agriculture has decreased significantly over the past few centuries. According to International Labor Organization data (via World Bank), agriculture employs just 1.36% of the US population. While labor participation is on a downtrend, productivity is rising. The use of modern equipment in farming has helped to achieve higher productivity with less labor. The importance of agricultural equipment will increase with even fewer people engaged in agriculture.
Equipment maintenance
You acquire equipment for your farm with a significant initial investment. To gain a good return on the investment, you need to use the equipment for a long time. To increase equipment lifetime, you need to perform regular maintenance activities. Agricultural equipment maintenance becomes a critical part of farm operations.
Another function of maintenance is to preserve the performance of equipment. During the use of equipment, it experiences wear and tear that affect its performance. Replacement of parts, topping up of lubricants and coolants, calibration, etc, should be done at regular intervals to maintain equipment performance.
Regular maintenance improves equipment availability. It is the percentage of time a piece of equipment is ready and available for use. Imagine you have to sow your seeds before it rains. It is forecasted to happen in a week. If sowing equipment is unavailable at the time, you will not be able to sow before it rains. It will ruin your farm cycle, and you will have to incur heavy losses. Regular maintenance helps increase machine availability and avoid a dire scenario.
Maintenance schedule
Agricultural equipment maintenance should be performed with discipline. You should create a maintenance schedule for your farm to accomplish that. Scheduled maintenance ensures that no maintenance activity goes unperformed. Weekly maintenance activities lie at the core of any sensible farm maintenance schedule. Maintenance tasks that are part of the weekly maintenance schedule are critical in maintaining smooth operations of your farm.
When you create a maintenance plan, you use all available information and create the plan that seems ideal. But the practicality and effectiveness of the maintenance plan come to light only when it is implemented. When the rubber hits the road, you will find that many ideas you thought were feasible fall apart. You will also find other challenges such as schedule clashes, lack of maintenance technicians, longer maintenance time, etc.
When there is incongruence between your maintenance plan and real-world implementation of it, you need to go back to the drawing board. You have to optimize the maintenance schedule to make it suited to your requirements and environment.
Metrics
Every maintenance plan you create should have a target to achieve. The maintenance metrics that have to be achieved need to be quantified. You can judge the success and failure of the equipment maintenance plan by comparing the results to the target. The maintenance metric you can use could be machine uptime, unscheduled downtime, efficiency, productivity, cost, safety, and other performance metrics. You need to choose the metrics that are relevant to your farm operations and judge the effectiveness of your maintenance plan.
Investigation
When you monitor the maintenance metrics, you will get to know the success or failure of your maintenance plan. Once you have identified the failure points, you should find out the reasons for the same. Conduct root-cause analysis to identify the underlying cause that led to the deviation from the targeted maintenance metrics. Your investigative process should not be limited to numbers and spreadsheets. You must get into the weeds and observe the maintenance activities being performed to identify the causes of failure. Once you have investigated all the failures and their causes, you can proceed to the next step in optimizing maintenance plans.
Reinvent
When you have the failure points and the reasons for that, you can create a new maintenance schedule to fix all the problems. Keep in mind to not introduce new failure points in the schedule. You can make use of Gantt charts to ensure that there are no scheduling conflicts. The new maintenance plan should be created after consultation with the maintenance technicians and experienced farm employees.
This maintenance plan can be implemented with a reliable Computerized maintenance management system (CMMS). CMMS can also help you in automating various maintenance processes. It has tools, such as checklists and SOPs, to help your team perform maintenance activities.
Maintenance kaizen
Kaizen is the Japanese lean manufacturing principle that is used extensively in various industries. The word Kaizen means continuous improvement. The same ethos has to be applied to agricultural equipment maintenance of your farm. You have reinvented a failed maintenance schedule. That is well and good. But no plan is perfect. Eventually, you will identify other faults and inconsistencies in the new plan. You always need the spirit to identify and investigate the new problems that will crop up. The optimization of the weekly maintenance schedule has to be a continuous never-ending process. It will deliver incremental performance improvement that compounds to a large gain over a long time.
–
Bryan Christiansen
Bryan Christiansen is the founder and CEO of Limble CMMS. Limble is a modern, easy-to-use mobile CMMS software that takes the stress and chaos out of maintenance by helping managers organize, automate, and streamline their maintenance operations.
Comments (0)
This post does not have any comments. Be the first to leave a comment below.
Featured Product
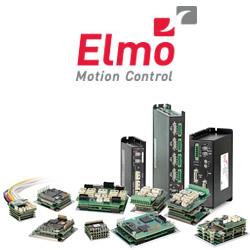