Developing Nondestructive Sensors for Quality Control
Farmers on the cutting edge of agriculture often use advanced techniques to evaluate their crops. Rather than cutting open fruit and sending the samples to a lab, some farmers have begun using nondestructive methods for quality control. This process can involve scanning vegetables with a sensor, inserting a needle into a plant stem, or punching a small hole out of a leaf to gather valuable data without destroying the harvest.
Problems With Traditional Monitoring Techniques
Evaluating crop quality isn’t a new process. However, traditional methods usually aren’t the most convenient. For example, farmers will dig up or pick a vegetable, cut it open, and ship it to a lab. After a waiting period, the lab will provide data regarding the crop’s sugar content, ripeness, age, or potential diseases. Farmers must take numerous samples to create an overall picture of crop health and maturity.
The farmers must rely on a third party to manage their own harvests. It costs money and fuel to ship the samples, and the farmers can’t control how long the waiting period is between shipping and getting lab results. It is time- and labor-intensive to pick multiple crops from the field, cut out specific pieces, package them for shipping, and drive them to the post office or another dropoff point.
Traditional methods destroy viable crops, which wastes food and reduces a farmer’s profits. With over 800 million people going hungry worldwide, minimizing food waste is essential.
Additionally, standard sampling methods often don’t catch problems with a harvest until it’s too late. Diseases or poor nutrient content may be too far advanced to manage by the time a farmer takes a sample.
Nondestructive Sensors Enter the Scene
It may sound futuristic, but advanced, nondestructive sensors have been around for a long time. X-rays and ultrasounds are perfect examples. Similar technologies evaluate the internal state of fruits, vegetables, leaves, and root systems to evaluate a plant’s health. These techniques are easy to use. Sometimes, they simply involve scanning crops without even touching them.
Nondestructive sensors can reduce travel time and therefore gasoline consumption because farmers no longer have to ship samples to a lab, saving money and reducing fossil fuel emissions. The sensors are a one-time expense – no more shipping crops over and over – and they give farmers more control over their own crop management.
Modern crop sensors allow farmers to catch problems quickly while there’s still time to manage them. They’re a highly accurate and efficient way to monitor plant health and optimize growth. They also complement other farming techniques like intercropping, crop rotation, and genetic modification. The information farmers gather from the sensors helps them determine when to harvest, store, and ship their crops.
How Nondestructive Sensors Work
There are two main types of sensors – those that detect internal states (in vivo sensors) and those that look at external signaling molecules, such as those on a plant’s surface or in the surrounding air. In vivo sensors are based on either electrochemical sensors or plant nanobionic sensors.
Both in vivo and external sensors analyze various chemical substances plants emit, called analytes, in leaves, fruits, juices, stems, and root exudates. External sensors can detect airborne metabolites such as volatile organic compounds (VOCs).
Farmers use sensors to measure the following analytes and more:
- Salicylic acid
- Hydrogen peroxide
- Tryptophan
- Abscisic acid
- Tannic acid
- 1-Naphthaleneacetic acid (NAA)
Electrochemical sensors often use voltammetry or chronocoulometry to take measurements. Nanobiotic sensors use near-infrared (nIR) fluorescence quenching, nIR fluorescence turn-on, and nIR fluorescence red-shift technology to peer inside plants.
The Benefits of Nondestructive Sampling Techniques
Thanks to nondestructive sensors, farmers have gained a new sense of control over their crop harvests. These sensors accurately detect problems, allow for quick management decisions, and save food and fuel to increase productivity. As agriculture increasingly relies on technology, nondestructive sensors will play a larger role on farms in the years to come.
Comments (0)
This post does not have any comments. Be the first to leave a comment below.
Featured Product
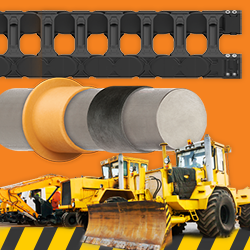