Driving the greenhouse industry to sustainable growth
Greenhouse farming is becoming increasingly popular, not least because it holds a number of key advantages over traditional farming methods. In fact, recent research by Precedence found that the global commercial greenhouse market was worth $34.8 billion in 2021 and is set to grow to $78.9 billion by 2030.
This boom in popularity is based on two factors. First, greenhouses eliminate the uncertainty of seasonal changes and weather to ensure closely controlled growing conditions. Second, and perhaps more importantly, as cities take up more and more of the available space for traditional farming, greenhouse growing enables production of fruit and vegetables to be carried out in urban areas, much closer to the point of consumption.
The challenge for commercial greenhouse operators is that they are often large and complex systems that require multiple processes to function harmoniously. Reliability and consistency are imperative here – if just one parameter goes outside the set limits, it could affect the balance of the entire system.
The irrigation process is particularly crucial, involving a variety of pumps, sprinklers and other equipment – all driven by electric motors which consume considerable amounts of energy. In the current era of energy shortages in some areas of the world, combined with increasing energy costs, particular attention must be paid to optimizing energy efficiency. In addition, water is also a valuable and often scare resource so its consumption must be carefully monitored and controlled to avoid any unnecessary waste.
Fortunately, due to recent developments in variable speed drives, also known as variable frequency drives, as well as in motors, and programmable logic controllers (PLC), greenhouse operators can now increase the energy efficiency and productivity of their equipment at the same time.
Enhancing performance and accuracy
Central to running a greenhouse is ensuring that all critical processes are fully optimized. This includes processes such as drip irrigation which ensures crops get a constant supply of water in exactly the right quantity. One of the most important elements of this is to regulate the water flow and pressure.
However, controlling the flow of water can be challenging. Pressure spikes can lead to water hammer – shockwaves that occur when a fluid in motion is forced to stop abruptly or change direction. This can cause damage to pipes, valves and sprinkler heads, ultimately shortening their lifespans and resulting in leakage. For example, a sprinkler head will not work correctly if the water pressure is too low, while if the pressure is too high it can pop off completely and need replacing. The resulting water loss from pressure-related issues can cause flooding, while even minor leaks impact both energy efficiency and operational costs.
Controlling pump motors with drives can safeguard against this by adjusting the water pressure constantly so that it is always at the optimal level. Built-in algorithms will protect against water hammer and cavitation, while low pressure detection will indicate leakage. The whole process can be automated via programmable logic controllers (PLCs) that excel at streamlining repetitive processes and are well-suited for use in drip irrigation.
Typically, water demand is high during the peak growing season, but there will be other periods when less water is needed. Drives allow for variable pumping so that the system can adapt to changing demand, optimizing water resources.
A further advantage of drives is their capability for intelligent pump control (IPC). This enables several pumps to be started and stopped as demand varies, without the need for an external controller.
Towards greater efficiency
Motor-driven pumps are one of the main sources of electrical energy consumption within greenhouses, along with lighting systems used to support crop growth and HVAC systems used for environment control.
When a motor is installed on its own it always runs at full speed, so that the output has to be adjusted manually by throttling. Using a drive enables the motor speed to be adjusted to meet the demand. Due to the relationship between speed and power usage, a relatively small decrease in speed can yield a very significant improvement in energy efficiency – for example, a pump running at half speed consumes only one eighth of the power.
This means that using a drive with a motor will typically cut energy usage by around 25 percent or more, but the savings can often be much greater. Furthermore, given the fluctuating costs of energy, the cost of installing drives can be paid back in just a few months.
Greenhouse systems will also benefit from having their motors upgraded. Many industrial motors in current use are rated below IE3, which is the current minimum requirement for all new motors installed within the EU. However, ultra-efficient IE5-rated motors based on synchronous reluctance (SynRM) technology are now available and they can reduce energy losses by up to 40 percent compared to IE3 models. It is not just a question of saving on operating costs; using high-efficiency motors and drives will also cut the carbon footprint of the greenhouse.
Enhanced control and safety
Drives offer a high level of controllability, including soft starting and stopping, that reduces stress on motors and other mechanical parts. Furthermore, an important feature of advanced drives is their capability to provide safety functionality such as safe torque off (STO).
This brings the motor to a controlled stop and ensures that it cannot re-started until the STO is removed, providing enhanced safety especially during inspection and maintenance.
Better decision-making through data
Advanced drives now have built-in sensors that monitor performance and energy usage during operation. Sensors can also be fitted to other equipment like motors and pumps, collecting performance and condition data to be stored and analyzed in the cloud. This provides the basis for fully-informed decision making for planned maintenance that maximizes uptime for increased productivity or to adjust operating parameters for improved energy efficiency.
Sustainable growth
Greenhouse farming is an ideal agricultural solution for increasingly urbanized populations, but operators face major challenges in terms of optimizing their energy consumption, cost-efficiency and overall productivity.
Embracing the latest data-driven drive and motor technology can help greenhouses to operate more sustainably to meet the world’s growing demand for fruit and vegetables.
For further information, please visit: https://new.abb.com/drives/segments/food-and-beverage/agriculture
Comments (0)
This post does not have any comments. Be the first to leave a comment below.
Featured Product
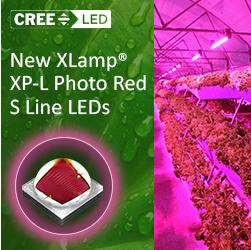