ELIMINATING THE NEED FOR SUBSTRATES - ENABLING CLEAN, SIMPLE AND RESILIENT GROWING
Tell us about GyroPlant and what you do?
GyroPlant was started in 2021 by our founder, Marcus. While originally designing a whole growing system, it became clear that substrates caused a major issue for the vertical farms with whom we collaborated. Two years of painstaking R&D later, we launched our flagship “GyroCup” product in early 2023. GyroCup is a reusable growing superstructure which eliminates the need for single-use substrates and plastic net pots. It offers indoor growers a range of benefits, including cost savings, yield improvement and cleaner conditions. Today, GyroPlant works with over 200 companies around the world. We pride ourselves on taking the most environmentally-conscious, user-friendly and performance-focused approach in the substrate business. We’ve also started to explore GyroCup’s potential in adjacent industries, including in space tech, plant propagation and pharmaceuticals.
What industry problem does your innovation address?
When we first explored the industry, we found it hard to accept the systemic use of disposable substrates. Even substrates that biodegrade are regularly shipped thousands of miles to farms. The ability to dispose organically doesn’t justify their single-use nature. Not only do single-use substrates add cost and uncertainty onto growers (for example, if supply chains are disrupted or prices change), they are environmentally damaging and unnecessary. The throwaway model of substrates might make some sense if growers were happy with their substrates – but they’re not!
We’ve taken a first-principles, low-tech inspired approach to solving the problem of substrates in indoor growing. From the very beginning, GyroCup has been reusable. This reduces input costs of replacing substrates and output costs of waste disposal. We found that growers usually mark substrates down as operational expenditure. But if they invest in our substrate replacement for the long-term, like they do with farm infrastructure more generally, they will see the payback in more ways than just cost. Due to GyroCup’s material composition, it provides a clean and consistent growing structure in which to grow. This not only further saves on cleaning materials and labour but reduces the risk of substrate contamination (both pests and diseases spreading across the farm via substrates and food impurities in food from the substrates). Ultimately, the quality of crops improves - which we all want to see. We often point to the sustainability credentials of our innovation (for example, growers save at least 80% of carbon emissions compared to the next best substrate). But as one grower remarked to us – “that’s obvious”.
How has your product been received so far?
We offer a radical solution to the often overlooked problems caused by substrates in indoor growing. That’s why we realise it can take a bit longer for growers to adopt our innovation in comparison to the more common substrates on the market. The shift towards GyroCup involves a process – growers need to understand the technology, they need to see how it works, and they need to trial it in their systems. Therefore, we establish a personal relationship with growers from their very first trial to large bulk orders. We don’t tell growers how they should grow, but we are always happy to give advice on growing techniques and procedures we’ve encountered from around the world. Having only just launched our product in March, we’re excited to say that over 200 companies, representing a huge variety of system set-up, are using GyroCup. To date, the most interest has been from small and medium sized farms, as large farms tend to invest in path-dependent growing infrastructure. But we've recently embarked on a significant R&D project dedicated to integrating GyroCup with automated processes – a highly sought-after solution for large farms.
What alternate uses for GyroCup are you exploring?
The more we collaborate with indoor growing companies, the more we learn about GyroCup’s various uses. We've received significant interest from the space tech sector, where a premium is placed on solutions that balance effectiveness with resource efficiency. Furthermore, GyroCup offers an opportunity to ensure quality and consistency in growing processes. This has led to its integration by growers catering to the pharmaceutical sector, a domain where the demand for high-quality ingredients is paramount for production. Another benefit of GyroCup lies in the elimination of the need to transplant seedlings into new substrates post-germination. This seamless continuity throughout the growth journey has proven to be a game-changer, particularly for growers in the plant and tree breeding industry. Due to the variety of crops it can grow, we like to think of GyroCup as a platform for growing. We’re always excited to see how growers employ our technology in various ways.
How do you see GyroPlant developing in the future?
We are a very pragmatic company, and we try to embody the design values which started it. We don’t see ourselves creating new product lines or venturing into designing whole cultivation systems. However, as mentioned previously, we have just started a large R&D project which will find new ways to integrate GyroCup into automated growing systems. Automation is crucial for the financial sustainability of the indoor growing industry and its ability to produce enough food to tackle food insecurity. Furthermore, we are encouraged by the broader shift towards sustainable growing practices. We see GyroPlant playing a key role in fostering this shift – collaborating with growers on integrating our innovation and promoting the most sustainable growing methodologies in the industry.
Comments (0)
This post does not have any comments. Be the first to leave a comment below.
Featured Product
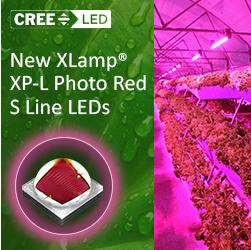